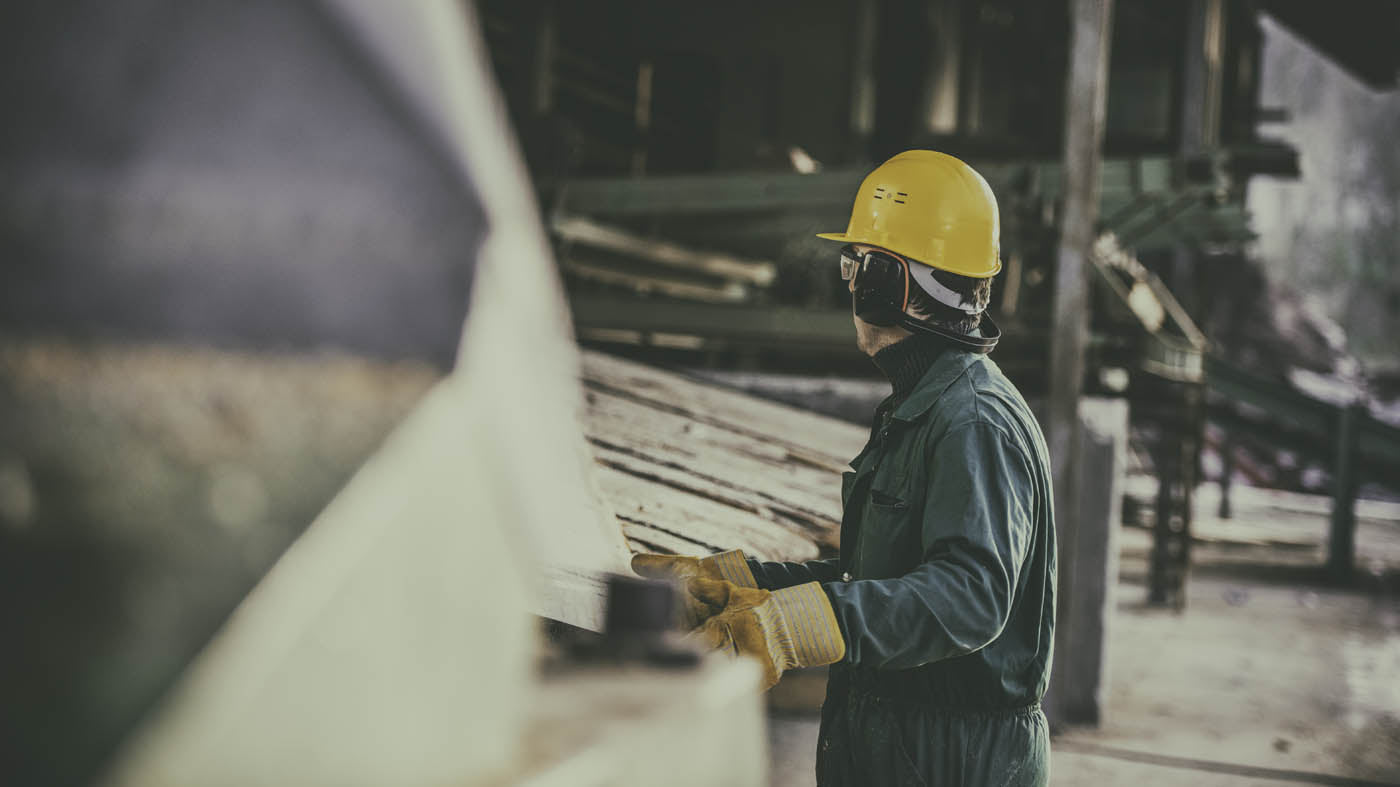
"Made in Germany"
since 1895.
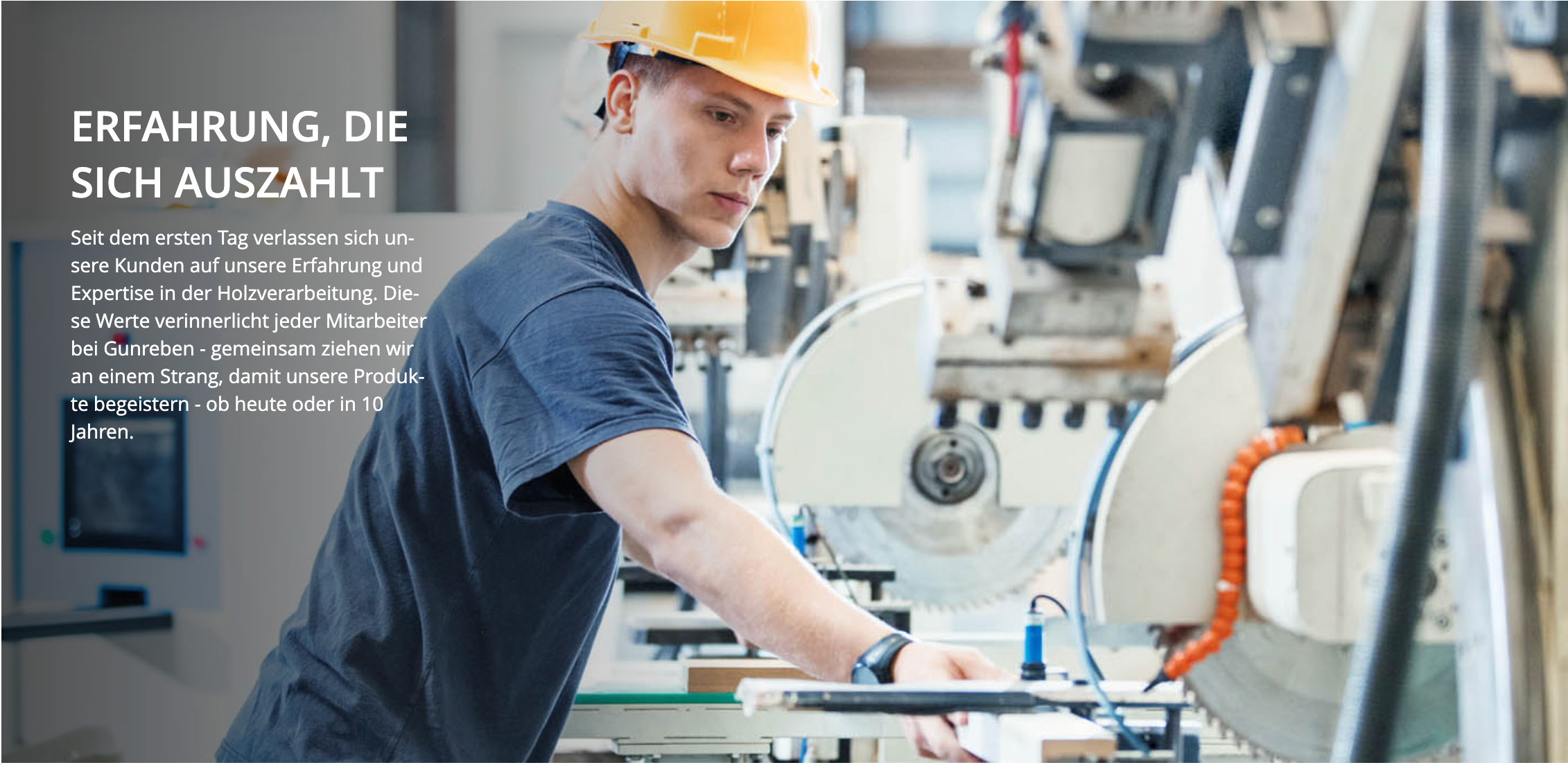
Area at the headquarters in Strullendorf
Volume in our drying chambers
Warehouse &
Production area
The log yard – looks simple, but it is not
At first glance, you might say it's just a pile of wood... But in fact, a system that has been sophisticated over many decades forms the basis of the first value-adding step in the Gunreben processing chain. Our roundwood purchasing department procures raw wood from private, municipal, and government suppliers throughout the purchasing season. Primarily oak, but also ash, beech, pine, spruce, red oak, and much more. In coordination with our sales department, log batches are transported from the forest to the log yard for processing as needed. Our regional partner companies transport the logs directly to our facility using the shortest possible route. Log haulage companies deliver up to 10 loads of logs to us daily from a catchment area of approximately 300 km around our site in 96129 Strullendorf, Germany. Each individual log is inspected and recorded upon delivery. We value our raw material and place great importance on ensuring complete traceability of the wood we process. To underscore our commitment to the sustainable management of German forests, we hold the PEFC and FSC® certifications. After incoming goods inspection, the logs are separated. The logs are visually inspected and sorted into different assortments according to internal quality guidelines. The logs are then cut to the required lengths using a machine. Any dents and defects are then smoothed out using a milling machine to ensure smooth sawing operations. The bark initially remains on the log to ensure the log retains its natural protective coating for as long as possible. The logs produced in this way are grouped into stacks according to quality, length, and diameter and stored in the log yard until further processing at the sawmill.
The sawmill - our heart of production
What was originally a sawmill focused on softwood processing has now evolved into one of Germany's largest hardwood sawmills for oak. In addition to the raw materials for our parquet and floorboard production, we also produce semi-finished products for trade and industry. Our lumber is valued in Germany and other European countries for its high drying quality and our customized grading. Our loose lumber, specially pre-sorted and optimized for industry, is prepared with care and expertise, just like our boules. Today, we manufacture products for further processing and retail on a gang saw line and a band saw line. The gang sawmill is fed with material using a forklift and a wheel loader. The first step involves removing the bark. Along with the bark, we also remove dirt and stones that could damage the tools of the downstream processing machines in our production facilities and at our customers' sites. After debarking, each log is individually fed into the gate. Attention is paid to curvature and defects to ensure the best possible quality and maximum board yield. The finished boards are sorted by the sorter into various automatically fed sorting boxes. If serious defects are detected, the boards can be cut to shorter lengths or directly cut to size for parquet flooring. This prevents inferior boards from being fed through the entire production process. Stacking slats are inserted between the layers of boards for subsequent drying before packaging. The board packages formed in the sawmill are brought directly to the sawn timber storage area by the forklift driver.
The band saw – for big things & oddballs
Our production and product range is complemented and rounded out by our band saw line. This extremely robust and reliable system allows us to respond to customer requests and the special requirements of very thick, crooked, and long logs. We can process logs with a log diameter of up to 1,200 mm and a length of up to 8,000 mm. Here, we produce sawn timber for tabletops, products for gardening and landscaping, and squared timber for exclusive roof trusses. The boards from this production line are also assembled into packages using a remote-controlled stacking machine, which are later pre-dried in the air in the lumber storage area.
The lumber yard – a guarantee for quality and reliable material supply
Neatly stacked and protected from the elements in the approximately 30,000 m² storage area, the wood is left outdoors for between six months and two years. The weathering removes the initial moisture from the wood and evens out the color of the sawn timber. This provides our processing department and our customers with a uniform, well-seasoned, and subsequently excellently kiln-dried product.
The drying chambers – 7,431.50m³ volume
Our drying kiln block has been continually expanded and modernized over the past decades. Today, we use state-of-the-art drying systems for our merchandise as well as for our own production. Our team of experienced specialists accurately dries every type of wood, whether hardwood, softwood, or tropical wood, to the desired final moisture content without causing tension or cracks that could damage the valuable product. We dry from 20 mm to 120 mm thickness, depending on customer requirements. The tropical woods for our decking production are also further dried here to the required final moisture content in order to exceed the usual quality on the market with our tropical wood decking "Made in Germany." We dry our lumber from the lumber storage area on a custom-order basis for resale to our customers.
The power plant – sustainability with its own electricity and heat
Sustainability isn't just about maximum yields. The near-complete utilization of the raw material wood, ideally at a single location, is the highest form of value creation. We only dispose of the ash at the end. We burn the bark in our own biomass cogeneration plant.
Cutting – dimensional accuracy in every step is the key to a top end product
At our cutting shop, a leading German machine manufacturer for wood processing, we process at least one truckload of boards daily into precisely prismatic cuts. Depending on the quality and dimensions of the semi-finished parts, these are later used to produce solid parquet, mosaic parquet, wood paving, country-style floorboards, lamparquet, and much more. In this step, our highly trained specialists process the lumber, which has previously been gently pre-dried in the air, into batches of identical semi-finished parts. These batches, then attached to stacking slats, are stored in the warehouse adjacent to the cutting shop. Depending on the order, these batches are also dried to the wood moisture content specified by DIN standards in drying chambers optimized for flooring production.
The Climate Hall – Wood processing takes time
All of our kiln-dried semi-finished products are temporarily stored in our 1500 m² climate-controlled warehouse. The combined control of humidity and room temperature over several weeks of storage results in a further optimization of the drying gradient of the wood moisture content. This ensures our customers receive a final product of the highest drying quality. From this warehouse, both the planing lines and the lumber sales staff are supplied with the products required for their orders.
The Planing Mill – Solid wood products for indoors and outdoors
In our planing mill, we can produce virtually all solid parquet and decking products known to the German and European markets on four planing lines. We specialize in the production of standard and custom-made solid parquet, solid wood floorboards, and decking. We offer the filling of wood defects with wood-colored or black filler and subsequent surface sanding with a grain size of 80/120, for example. We can also treat the parquet and decking with oxidative and hard wax oil. Even unusual wood moisture levels for unusual locations, such as brewery buildings, are no challenge for us. Our decking boards are manufactured to order in at least five different surface combinations, entirely according to our customers' wishes. All of our products undergo internal quality control by our machine and plant operators before being transported to the customer or to our warehouses.
Sawn timber measurement – Wood is a natural product and is perceived differently by each customer
After drying and storage in our climate-controlled hall, the lumber is qualified and measured for our customers on a case-by-case basis. We know our customers and their needs, often for decades! Our customers rely on us to not only deliver the desired quality, but also ensure that the lumber we supply is optimally suited to our customers' end products. Remote-controlled vacuum stacking machines are used to present the boards to the lumber measurer and then stack them. Our customers receive a measurement report for each package to ensure maximum transparency and traceability. We either deliver the products directly to the customer or store them until they are picked up. Service and quality are at the heart of our business.
Wholesale warehouse – We keep stock!!!
In our over 40,000 m² warehouse at our headquarters in Strullendorf, we operate a highly stocked warehouse. We are committed to maintaining large quantities of raw materials, semi-finished parts, and finished products for our customers. All of our warehouses are heated both summer and winter. However, our material, wood, is a natural product, and it takes time to manufacture finished products of high quality.
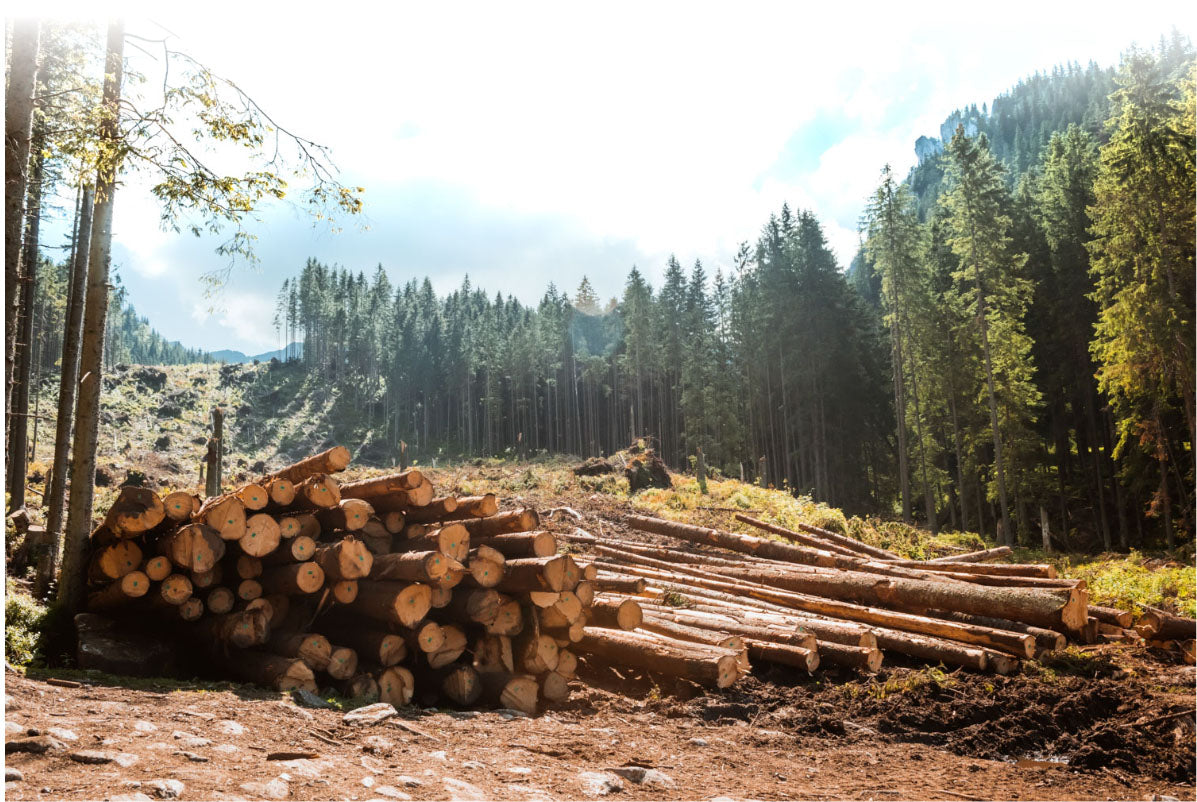